Industrial Automation
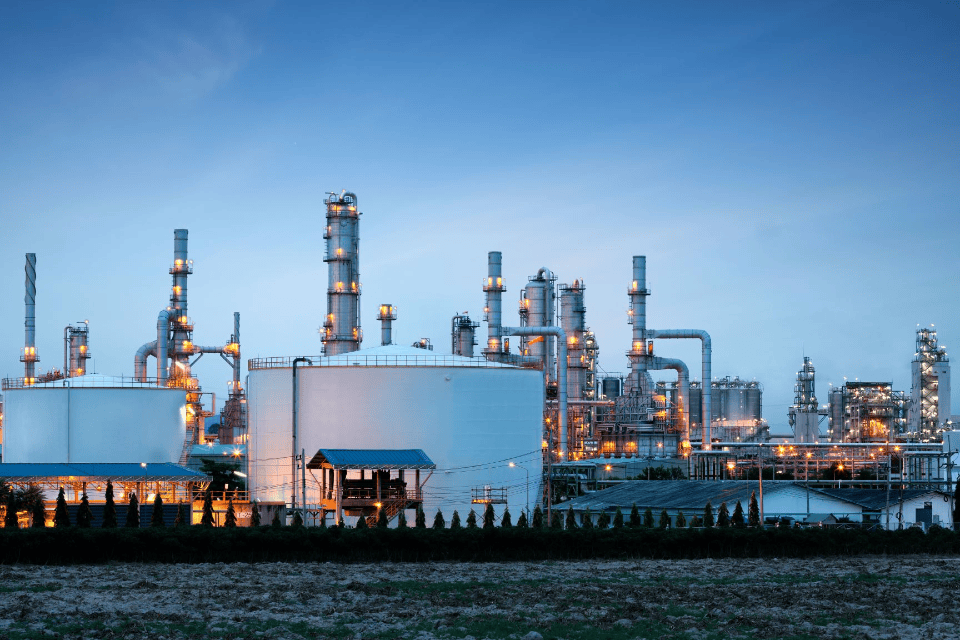
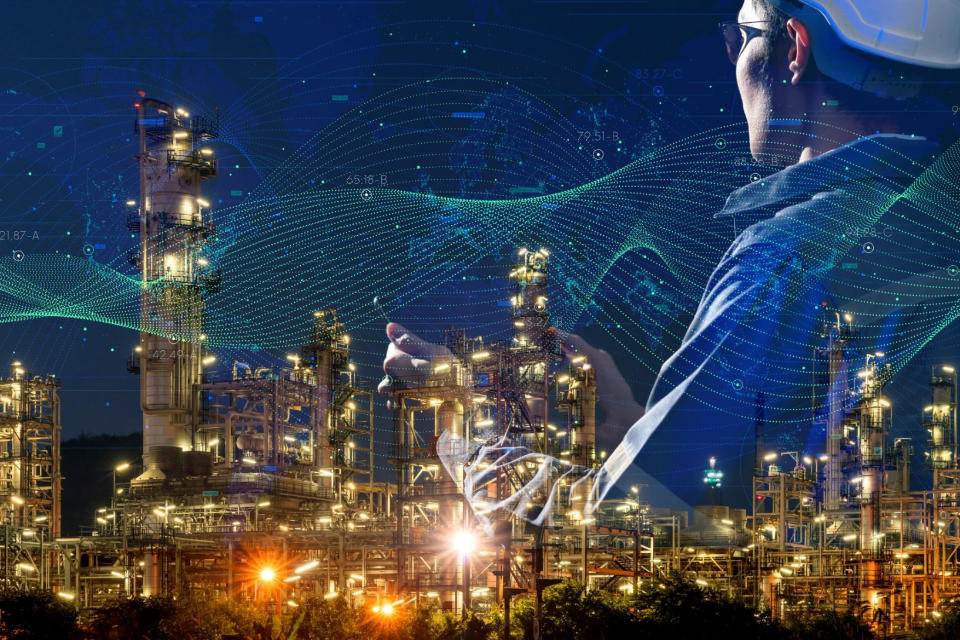
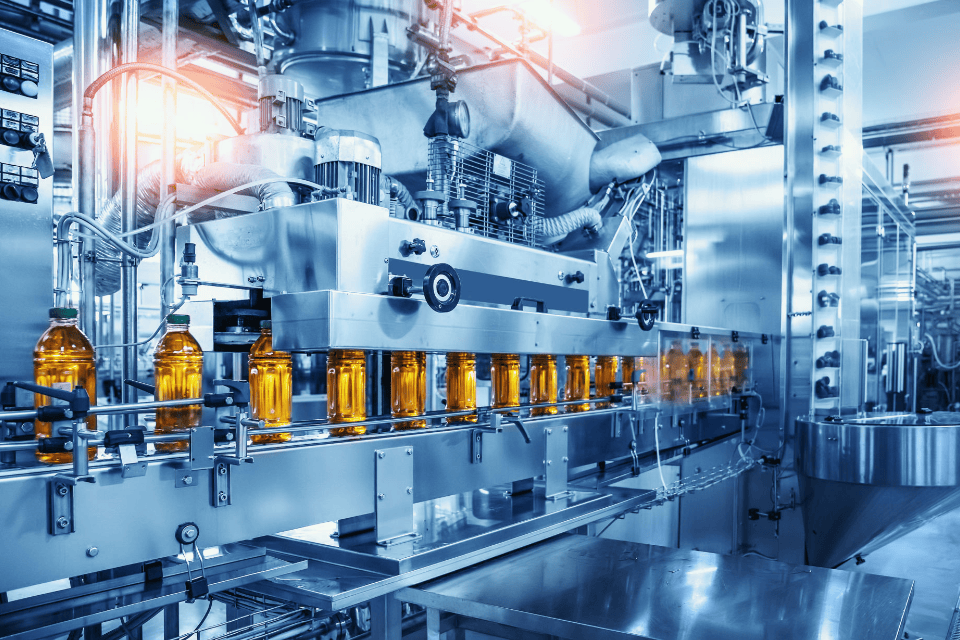
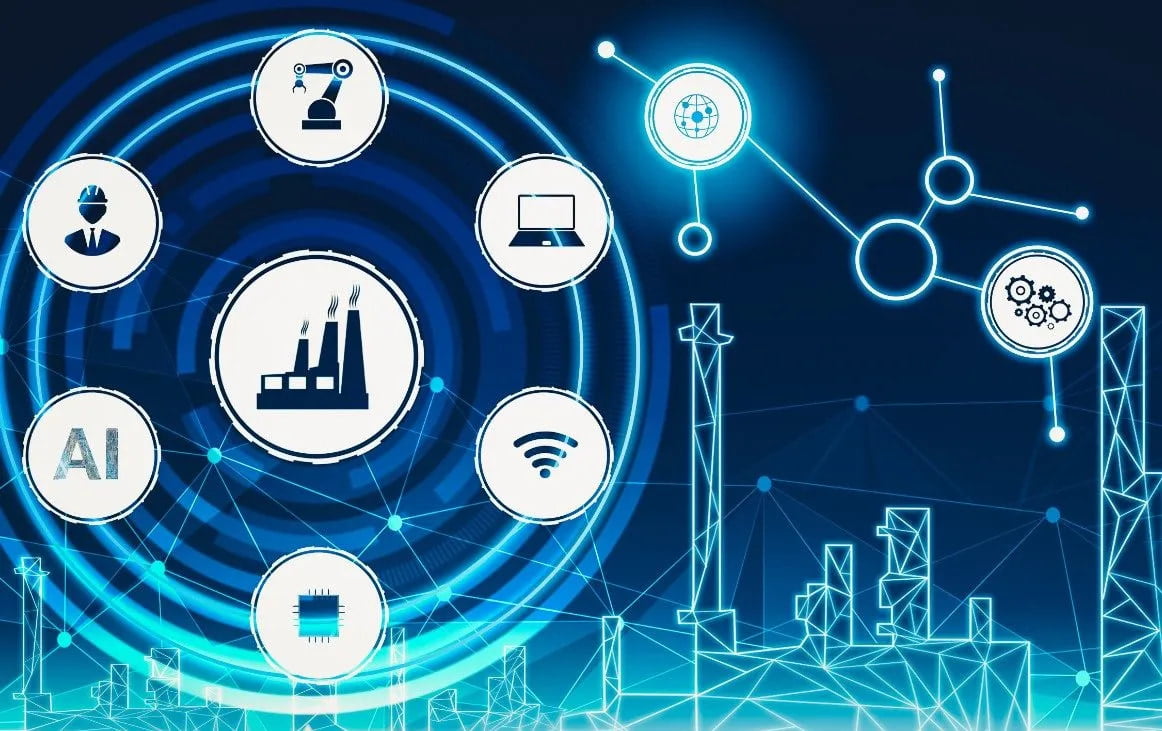
Leveraging our expertise across multiple automation platforms, we deliver industrial automation solutions using a range of control systems, including PLC & DCS. Our solutions enable the control of various operations with minimal human intervention. By applying sophisticated control strategies and technologies, we ensure that the automation system becomes an integral and efficient part of your industry and domain, achieving optimal performance and output.
Industrial automation services encompass a range of solutions designed to improve manufacturing efficiency, productivity, and safety by automating industrial processes. These services often include:
- System Design and Integration: Tailoring automation systems to specific manufacturing needs, including selecting and integrating hardware (sensors, actuators, controllers) and software (SCADA, MES).
- Process Automation: Implementing and optimizing control systems to automate repetitive tasks, such as assembly lines, packaging, or quality control.
- Control Systems Engineering: Designing and programming control systems, such as PLCs (Programmable Logic Controllers) and DCS (Distributed Control Systems), to manage and monitor industrial processes.
- Data Acquisition and Analytics: Collecting and analyzing data from industrial processes to optimize performance, predict maintenance needs, and improve decision-making.
- Maintenance and Support: Providing ongoing maintenance services, troubleshooting, and support to ensure the automation systems run smoothly and efficiently.
- Training and Consultation: Offering training programs for staff on new systems and technologies, and consulting services to help businesses identify automation opportunities and solutions.
- Cybersecurity: Implementing security measures to protect industrial control systems from cyber threats and ensure data integrity.
- Retrofit and Upgrade Services: Updating or retrofitting existing systems with new technologies to extend their lifespan and improve functionality.
- Project Management: Overseeing the entire automation project lifecycle, from initial planning and design through to implementation and post-installation support.
These services are crucial for industries looking to enhance their operational efficiency, reduce downtime, and stay competitive in the market.
IoT & cloud SCADA
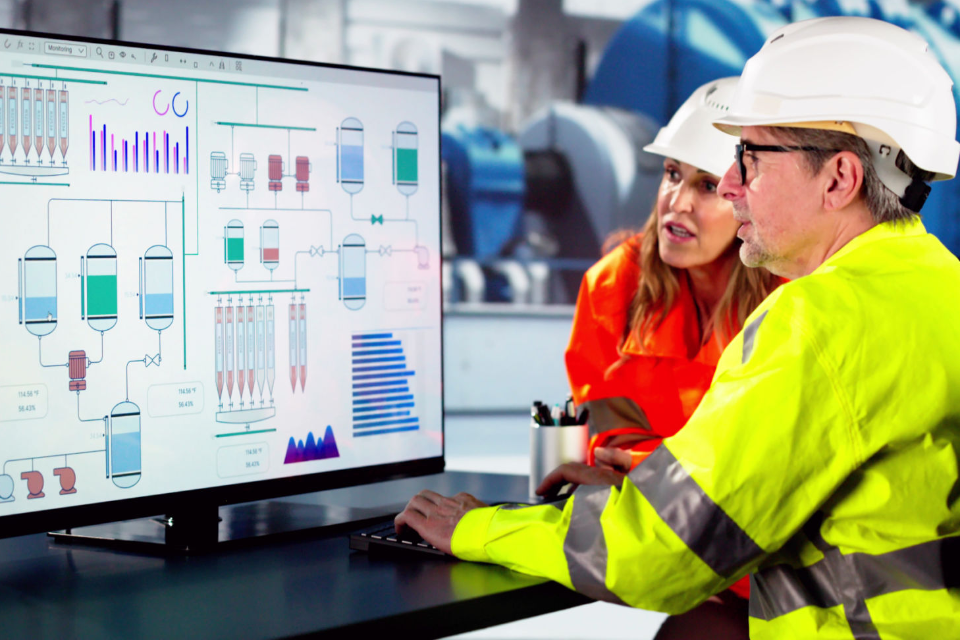
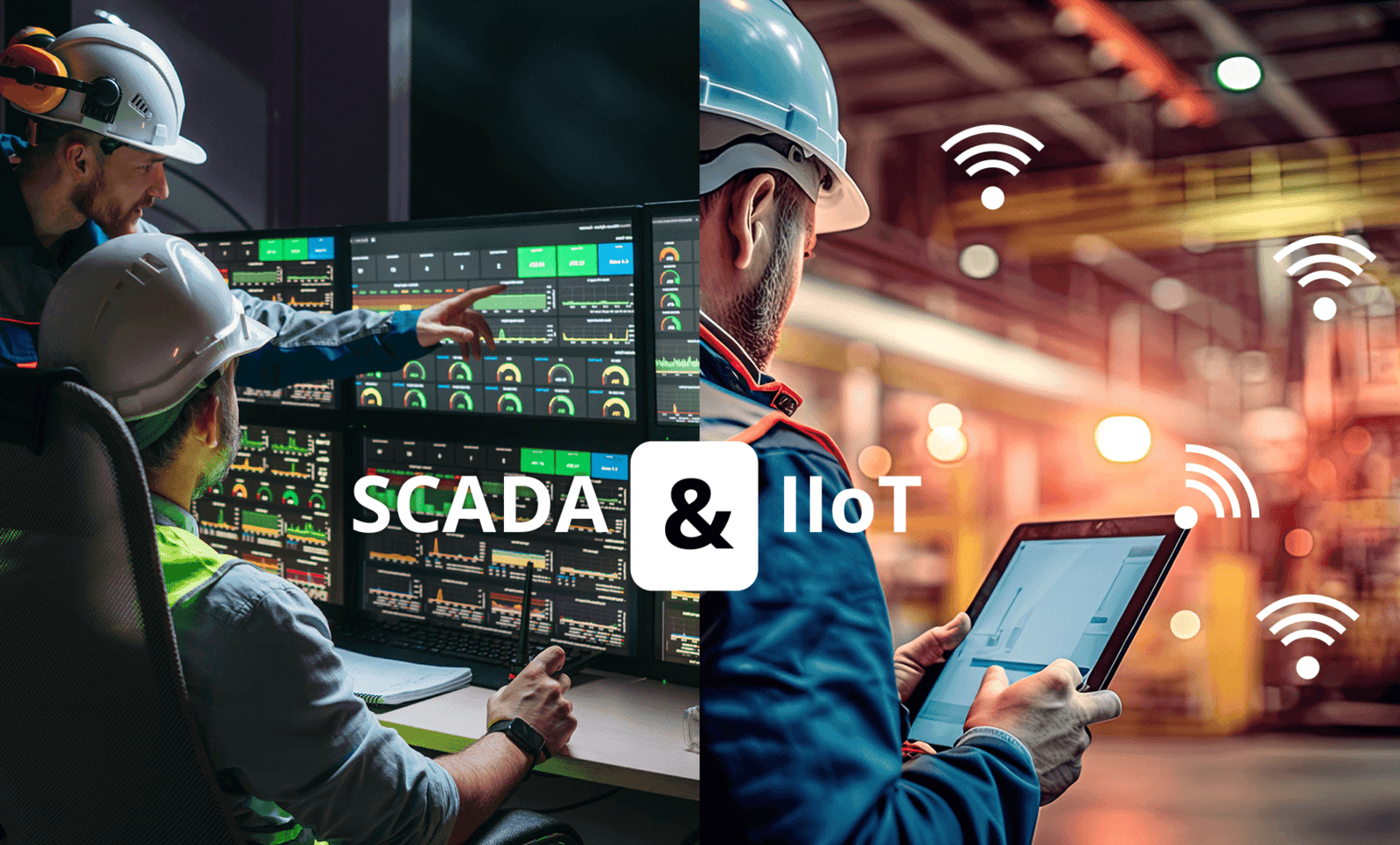
The Internet of Things (IoT) and cloud-based SCADA systems are crucial in industrial automation, offering the ability to monitor and control entire operations from virtually anywhere. Their primary goal is to foster cooperative communication and interaction within the manufacturing, construction and facility management sectors. Our robust system is designed for flexibility and scalability, allowing you to manage and adapt your operations effectively while working within a limited budget.
Integration of IoT & Telemetry;
- Enhanced Monitoring: IoT devices can provide telemetry data to centralized systems for comprehensive monitoring and control.
- Improved Decision-Making: Combining real-time telemetry data with IoT analytics enables more informed decision-making and faster response times.
- Operational Efficiency: Automation of data collection, processing, and reporting reduces manual intervention and increases operational efficiency.
- Predictive Maintenance: IoT sensors and telemetry data can be analyzed to predict equipment failures and schedule maintenance before issues occur.
Fleet Management System
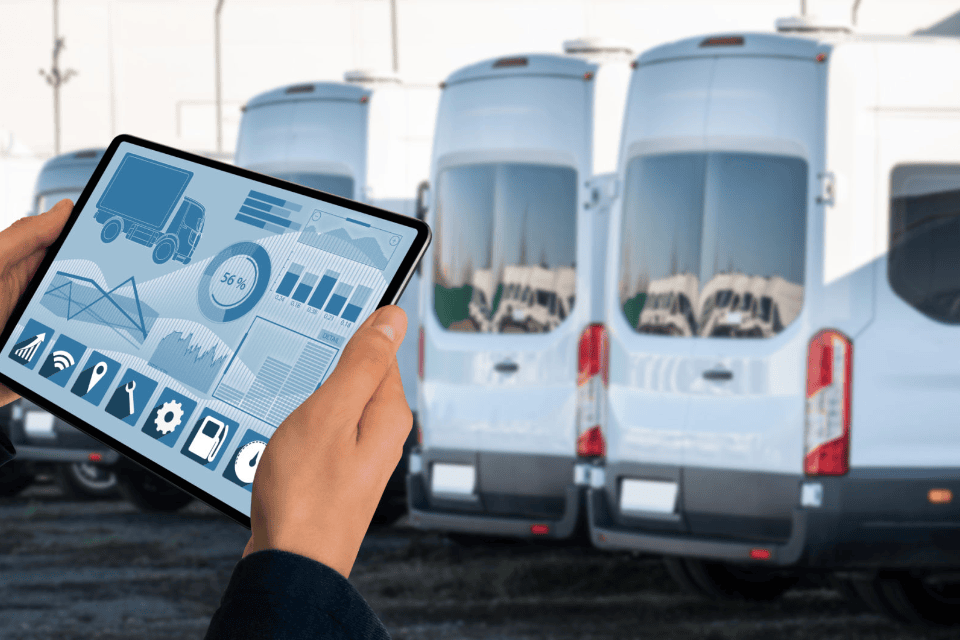
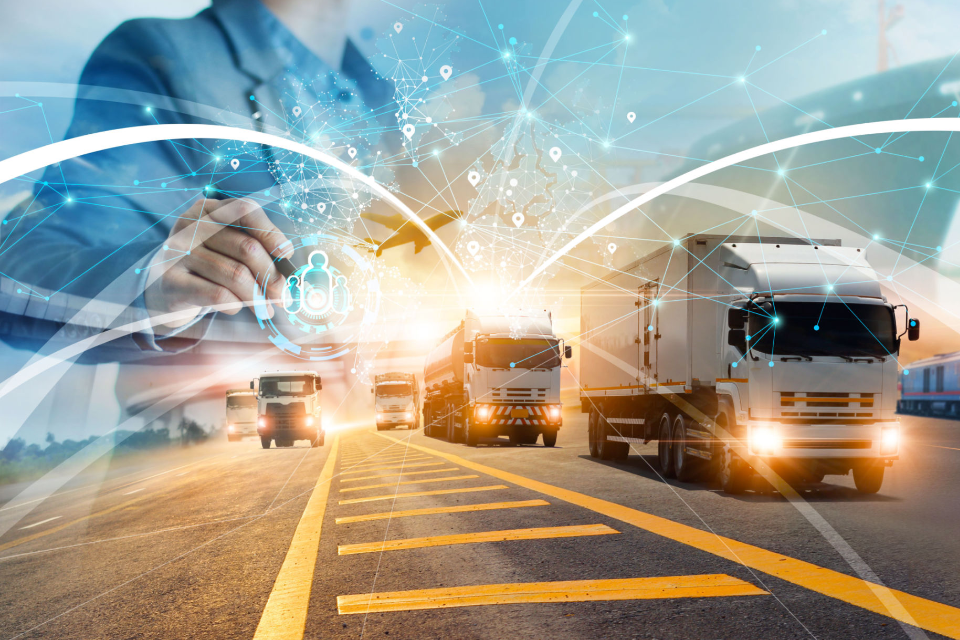
1. Vehicle tracking 2. Fleet maintenance 3. Driver management 4. Fuel management
5. Routing & dispatching 6. Reporting & analysis 7. Alerts & notifications
8. Compliance management
Benefits of a Fleet Management System
- Enhanced Efficiency: Optimizes routes and schedules, leading to reduced fuel consumption and improved delivery times.
- Cost Reduction: Lowers operating costs through better fuel management, reduced maintenance expenses, and minimized downtime.
- Improved Safety: Monitors driver behavior and provides safety training, reducing the risk of accidents and enhancing overall road safety.
- Better Compliance: Ensures adherence to regulatory requirements, helping to avoid fines and legal issues.
- Increased Productivity: Streamlines operations with automated tools for scheduling, dispatching, and tracking, allowing for more effective resource allocation.
- Real-Time Insights: Provides real-time visibility into fleet operations, enabling proactive decision-making and problem-solving.
- Environmental Impact: Helps in reducing the fleet's carbon footprint through efficient fuel usage and optimized routes.
Fuel Monitoring System
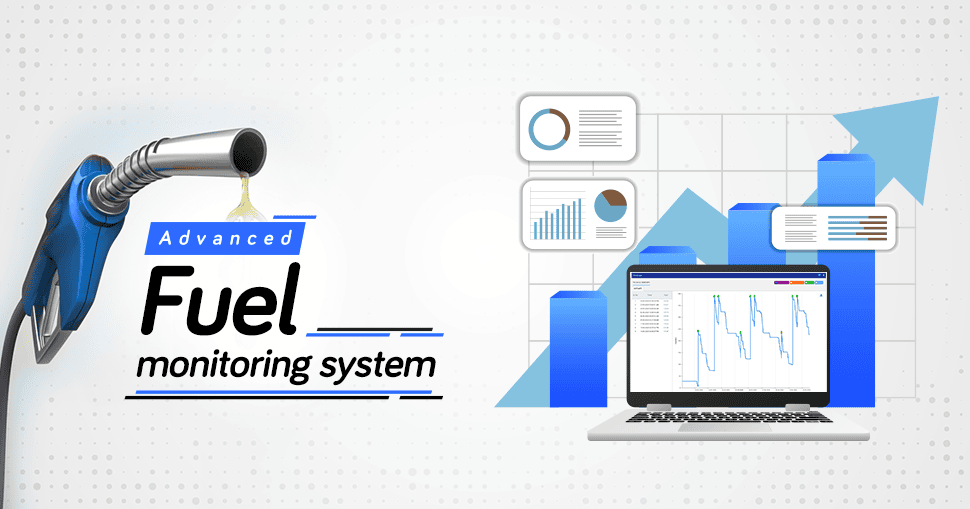
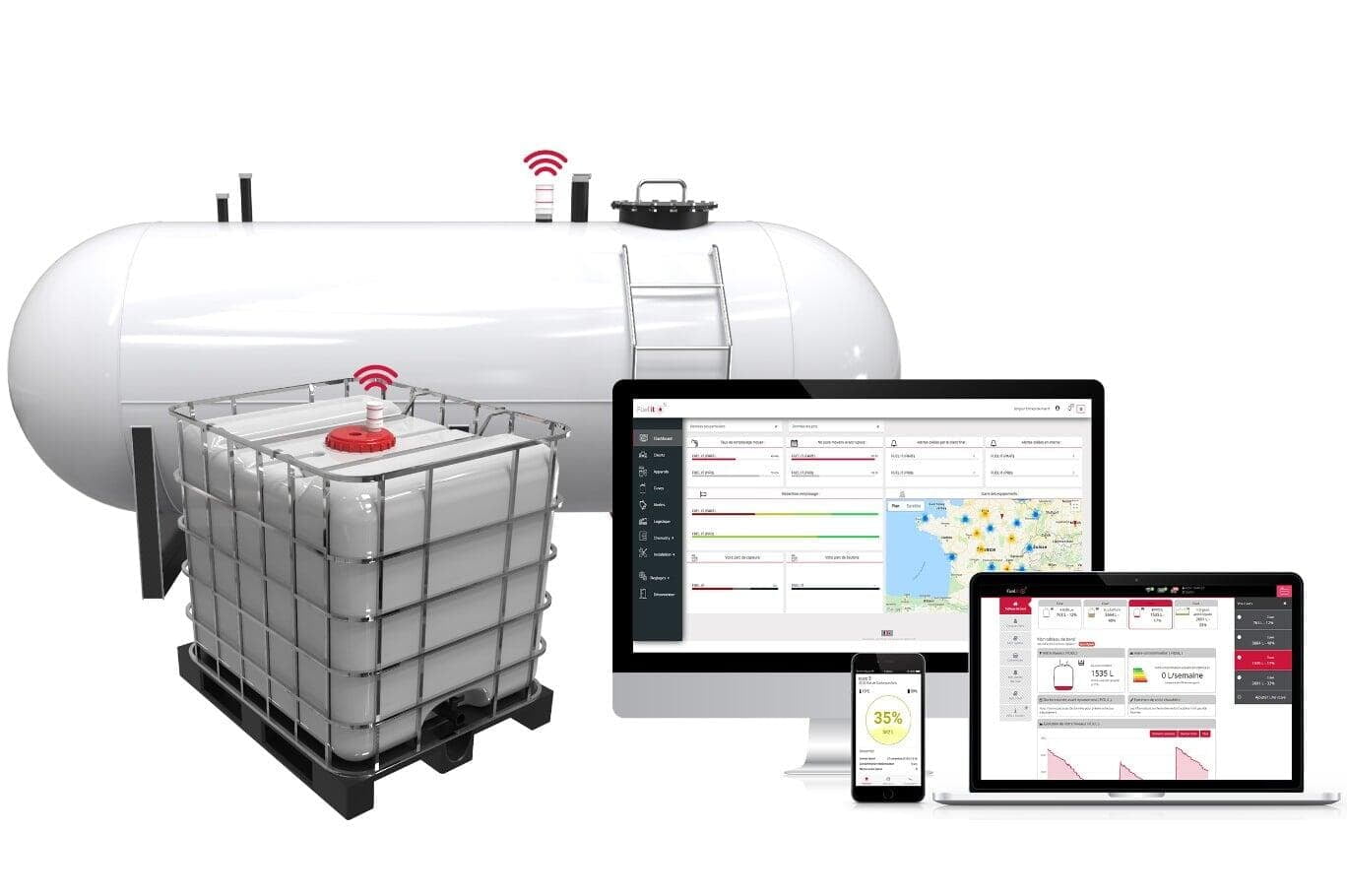
Benefits;
- Real-Time Monitoring: Provides immediate visibility into fuel levels and usage, helping to prevent theft and ensure efficient fuel usage.
- Cost Savings: Reduces unnecessary fuel consumption and prevents overfilling or underfilling, which can lead to cost savings.
- Operational Efficiency: Enhances planning and logistics by providing accurate data on fuel needs and usage patterns.
- Maintenance and Safety: Early detection of potential issues such as leaks or equipment malfunctions, which can prevent costly repairs and ensure safety.
- Environmental Impact: Helps in reducing fuel wastage and optimizing fuel usage, which can contribute to a lower carbon footprint.
Electrical Control panels
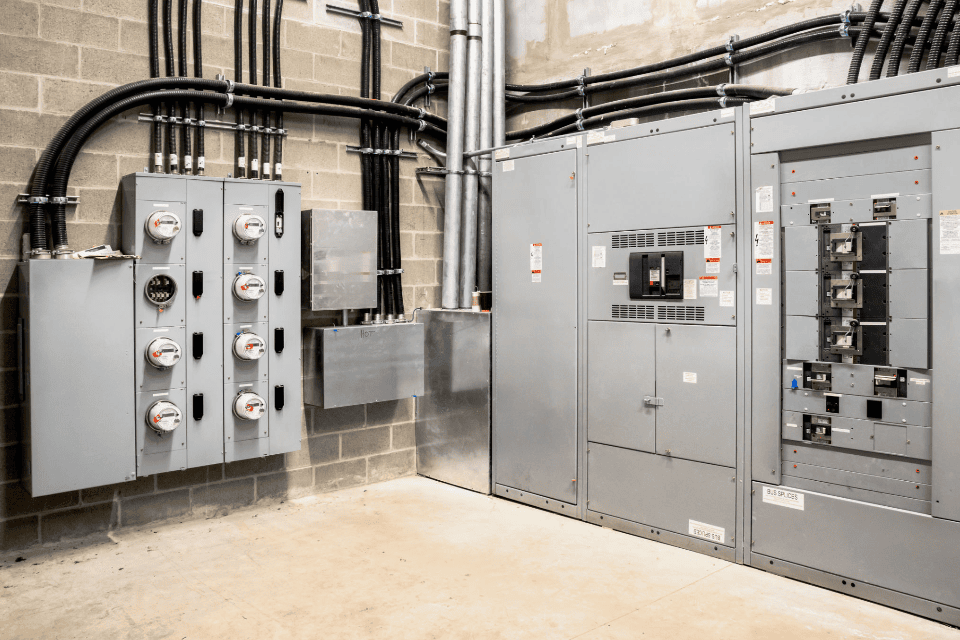
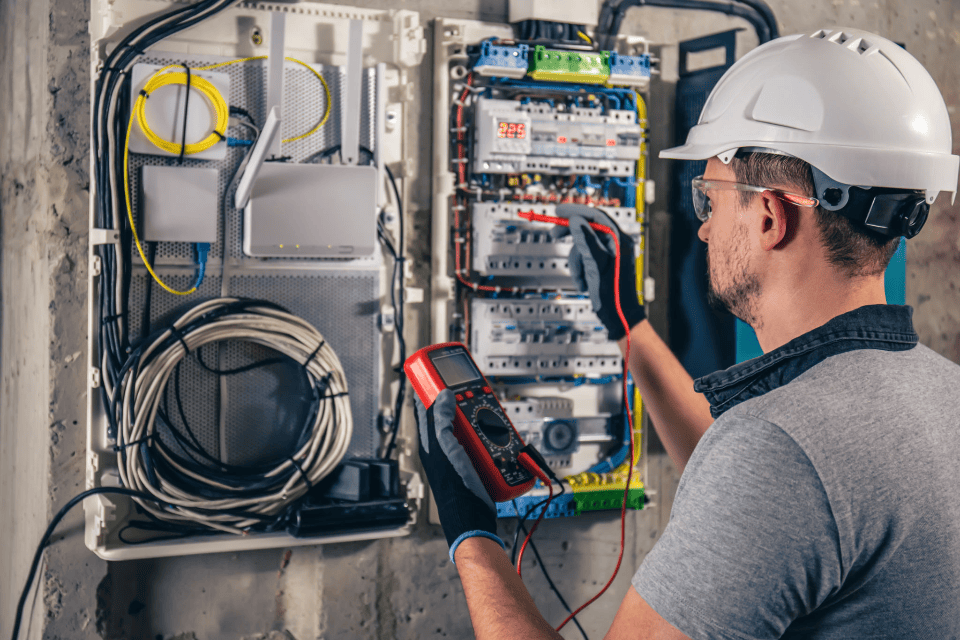
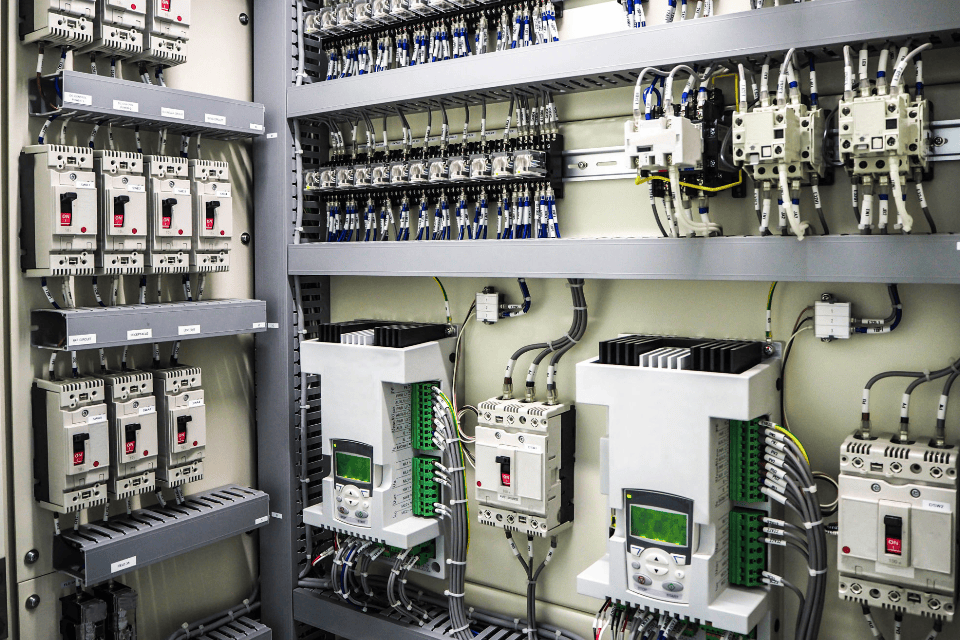
Here’s a comprehensive overview of control panels supply and services:
Control Panels Supply
- Electrical Control Panels: Manage electrical circuits, protect equipment, and ensure proper power distribution.
- PLC Panels: House programmable logic controllers (PLCs) for automation and control of industrial processes.
- SCADA Panels: Support supervisory control and data acquisition (SCADA) systems for large-scale process control and monitoring.
- Motor Control Centers (MCCs): Control and monitor electric motors in industrial settings.
- HVAC Panels: Manage heating, ventilation, and air conditioning systems.
Control Panels Services
- Design and Engineering
- Manufacturing and Assembly
- Installation
- Programming and Configuration
- Testing and Commissioning
- Maintenance and Support
- Compliance and Certification
Instrumentation & Control products
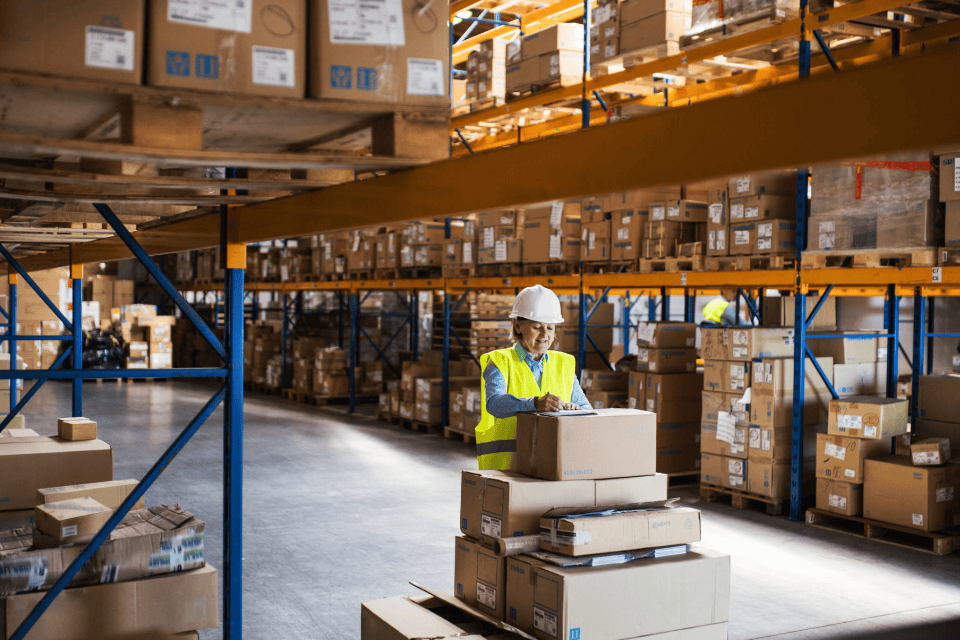
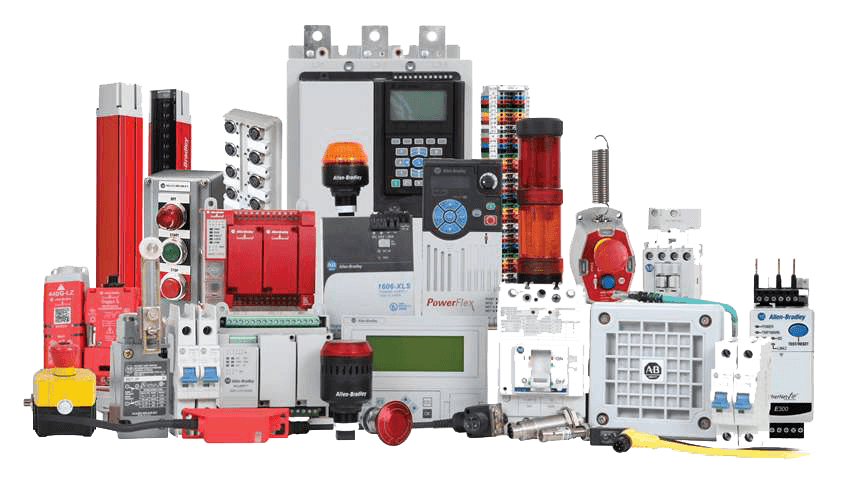
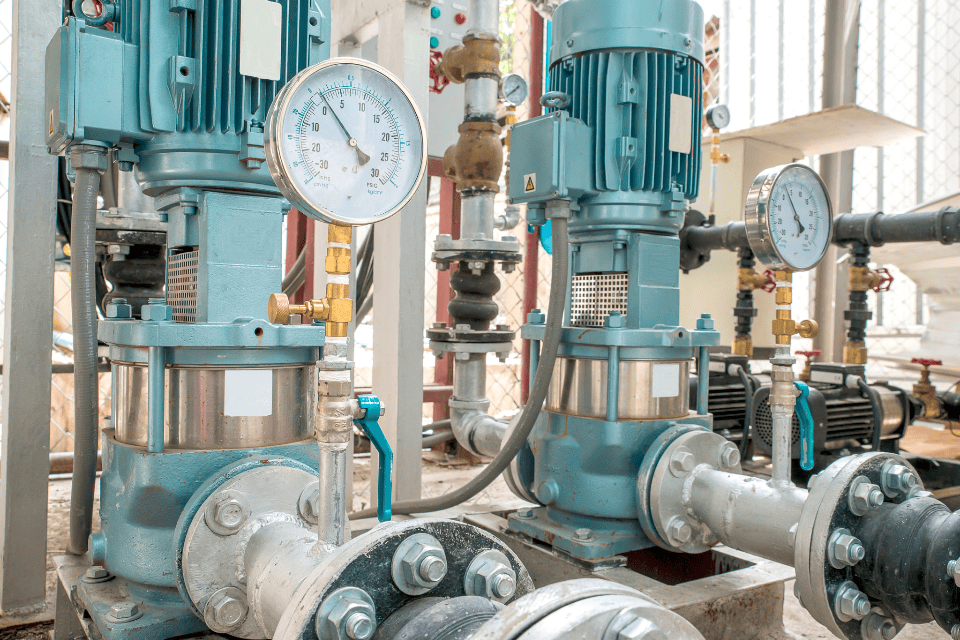
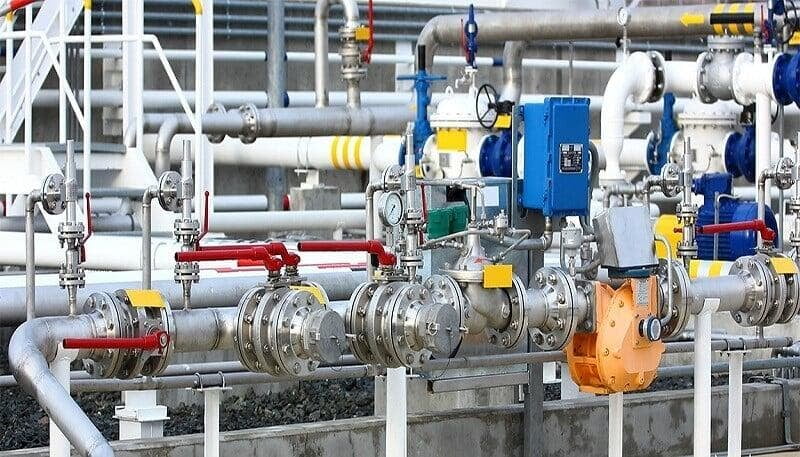
Types of Control and Instrumentation Products
- Sensors:
- Temperature Sensors: Measure temperature in various applications (e.g., thermocouples, RTDs).
- Pressure Sensors: Monitor pressure levels in gases and liquids.
- Level Sensors: Detect the level of substances (e.g., capacitive, ultrasonic, radar).
- Flow Sensors: Measure the flow rate of liquids or gases (e.g., electromagnetic, turbine).
- Transmitters:
- Pressure Transmitters: Convert pressure measurements into an electronic signal.
- Level Transmitters: Provide continuous level measurement and transmit data.
- Temperature Transmitters: Convert temperature readings from sensors into a standardized signal.
- Controllers:
- Programmable Logic Controllers (PLCs): Automate processes by controlling machinery based on input signals.
- Distributed Control Systems (DCS): Manage and control complex processes across multiple locations.
- Temperature Controllers: Regulate temperature by controlling heating or cooling elements.
- Indicators and Displays:
- Digital Indicators: Show measurements from sensors (e.g., digital readouts for temperature, pressure).
- Graphic Displays: Provide visual representations of process data and trends.
- Alarm Panels: Alert operators to abnormal conditions or process deviations.
- Actuators:
- Electric Actuators: Control mechanical movements using electric power.
- Pneumatic Actuators: Use compressed air to move or control equipment.
- Hydraulic Actuators: Utilize hydraulic fluid for heavy-duty movements.
- Switchgear:
- Circuit Breakers: Protect electrical circuits from overloads and short circuits.
- Contactors and Relays: Switch electrical circuits on and off.
Repair of Industrial products
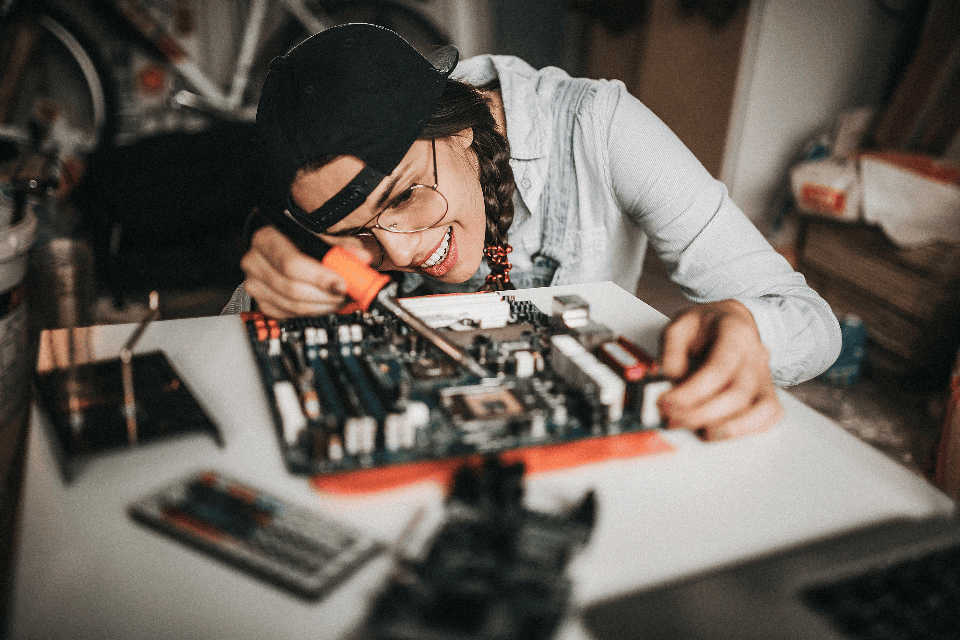
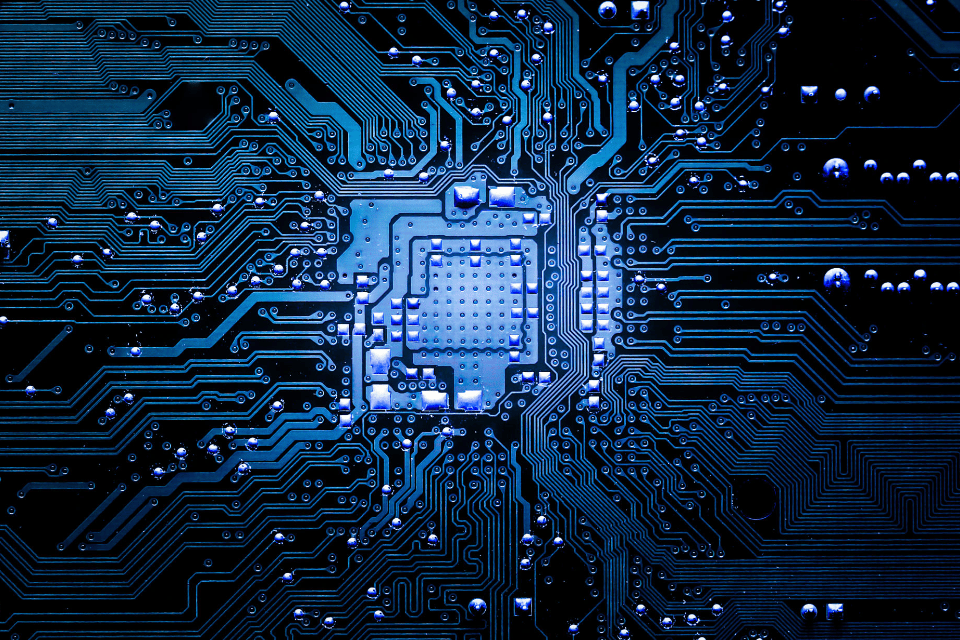
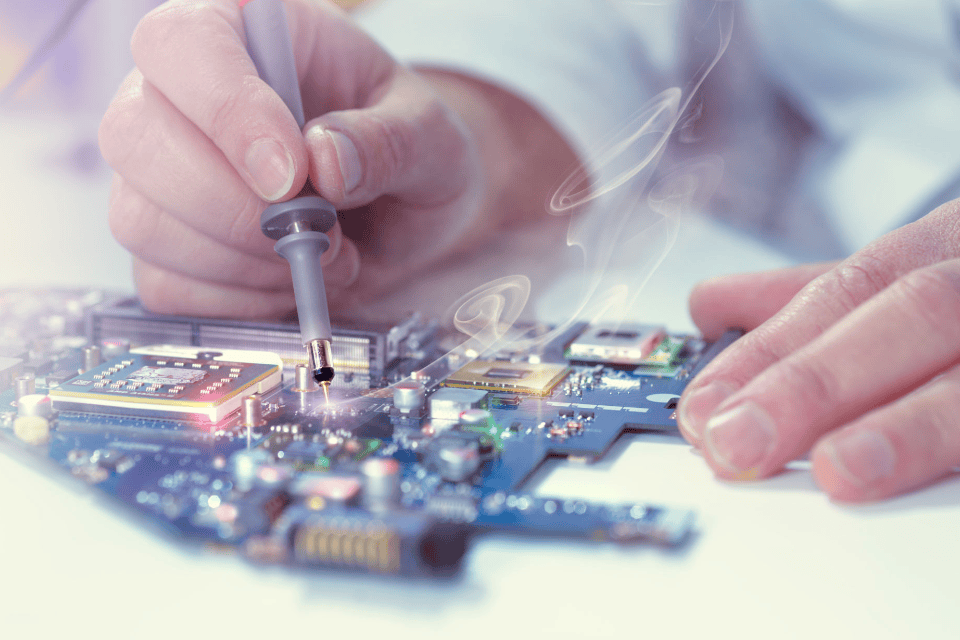
Common Industrial Control Products and Their Issues
1. Variable Frequency Drives (VFDs):
- Common Issues: Overheating, fault codes, electrical failures, parameter setting errors, component wear.
- Symptoms: Motor performance issues, error codes on display, overheating, erratic operation.
2. Programmable Logic Controllers (PLCs):
- Common Issues: Communication failures, I/O module failures, processor failures, power supply issues, software errors.
- Symptoms: Loss of communication, I/O malfunction, PLC crashes or resets, unexpected behavior in automation.
3. Human-Machine Interfaces (HMIs):
- Common Issues: Display failures, touch screen issues, communication problems.
- Symptoms: Unresponsive touch screens, display errors, issues with data updates.
4. Sensors (e.g., temperature, pressure, flow):
- Common Issues: Sensor drift, calibration errors, physical damage.
- Symptoms: Incorrect readings, inconsistent data, physical wear or damage.
5. Control Panels:
- Common Issues: Wiring faults, component failures, outdated controls.
- Symptoms: Electrical failures, inconsistent performance, physical damage to components.
6. Actuators (e.g., electric, pneumatic, hydraulic):
- Common Issues: Mechanical failure, control signal issues, air or fluid leaks.
- Symptoms: Inaccurate or failed movements, noise, leakage.
Engineering Consultancy
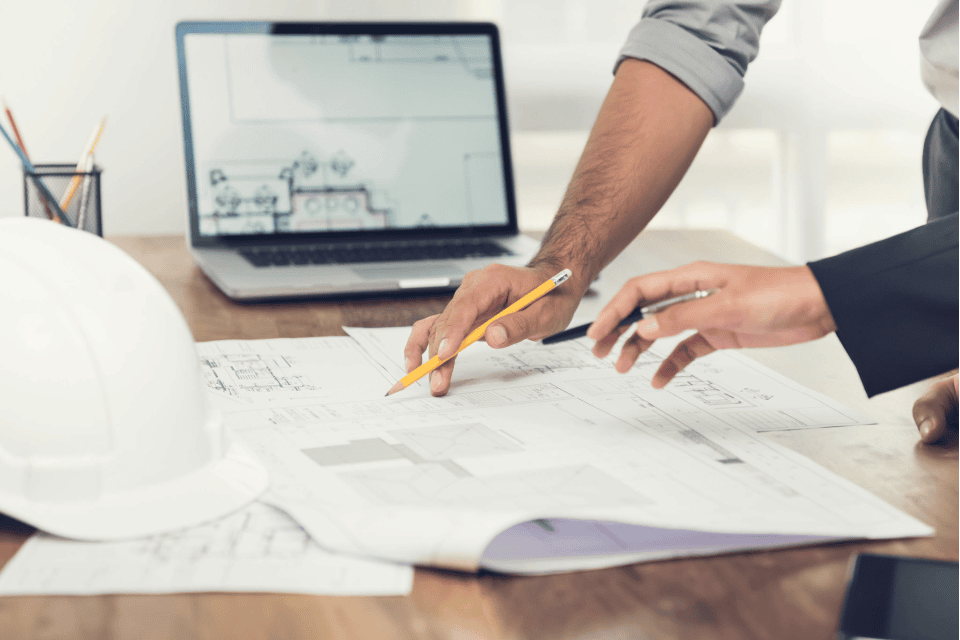
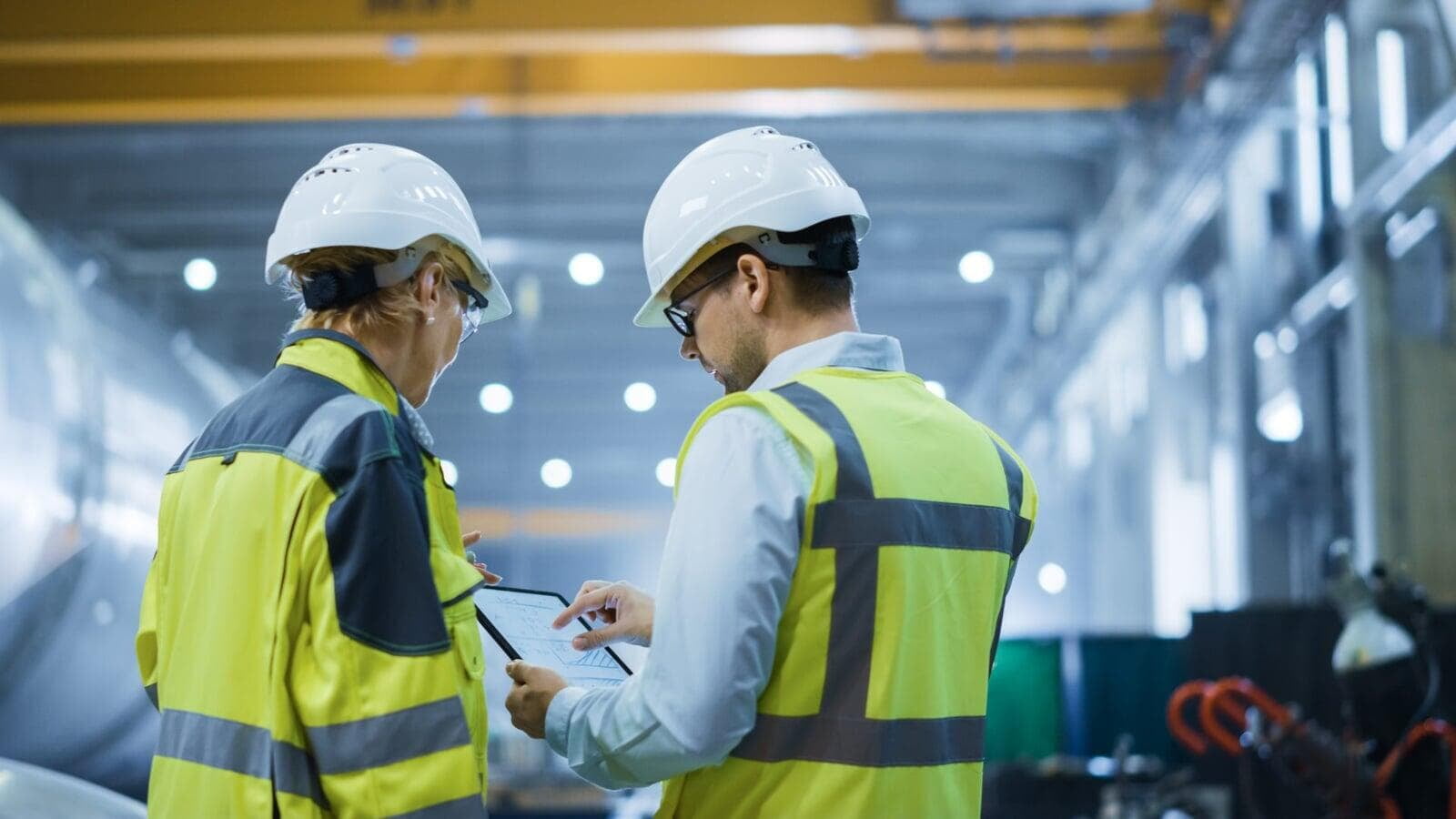
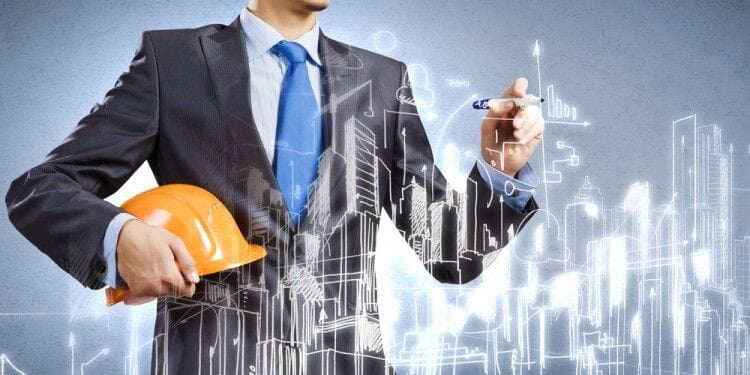
- Feasibility Studies: Assess the viability of projects and solutions, including cost-benefit analysis and risk assessment.
- Design and Engineering: Develop detailed designs and engineering solutions tailored to project requirements.
- Project Management: Oversee project execution, manage resources, and ensure timely delivery within budget.
- Technical Analysis: Conduct detailed technical analysis to solve complex problems or optimize existing systems.
- Regulatory Compliance: Ensure projects comply with relevant regulations, standards, and codes.
- Troubleshooting and Diagnostics: Identify and resolve technical issues or inefficiencies in existing systems.
- Optimization and Efficiency Improvement: Enhance performance and efficiency of systems and processes through analysis and redesign.
- Training and Support: Provide training for staff and ongoing support for implemented solutions.
- Risk Management: Assess and mitigate potential risks associated with engineering projects or systems.